Performing a surface finish is critical for a PCB as it prevents the copper from oxidation. The process helps in forming a reliable connection between the electronic component and the board. Major functions of the surface finish include preparing the surface for soldering associated components during assembly and preventing any exposed copper (including ground plains, pads, holes, and traces) from deteriorating.
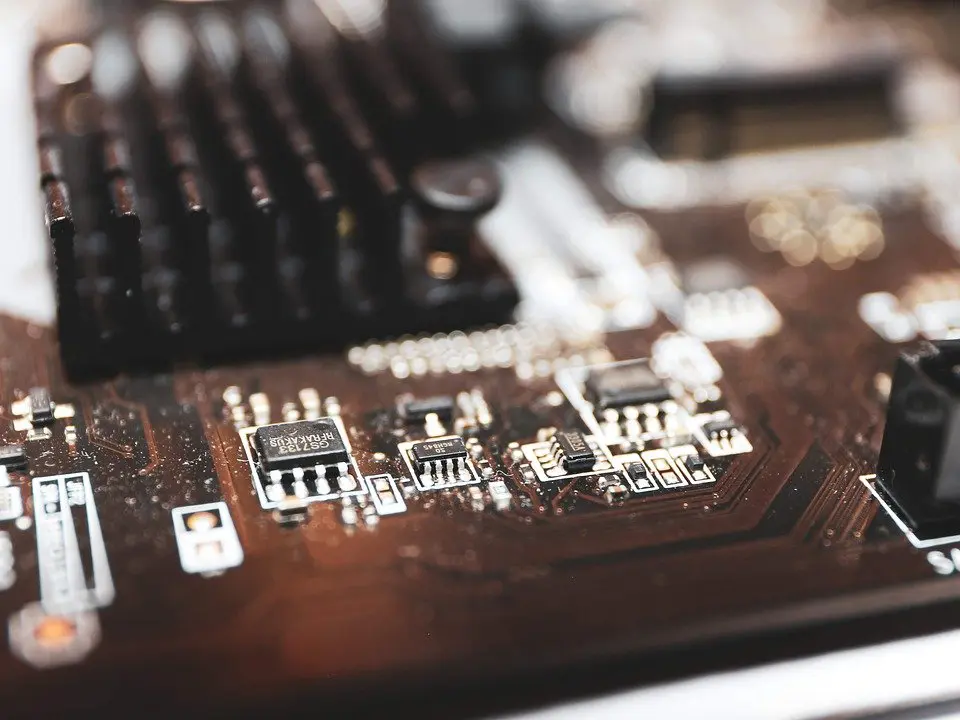
(Pixabay / ArtificialOG)
There are various PCB surface finish types, and each type comes with its benefits and shortcomings. Choosing the right surface finish for your design requires a good understanding of the different options. Below are the most popular types of surface finishes that help fulfill varying project requirements.
Electroless Nickel Immersion (ENIG)
ENIG is fast becoming the surface finish of choice in the PCB industry. It’s basically a “double layer” metallic coating that features nickel, which acts as both a surface to which components will be soldered and as a barrier to the copper. The nickel is secured by a layer of gold during storage. This surface treatment is the answer to various industry developments such as the rise of complicated surface components that demand flat surfaces (like flip chips and BGAs).
Why You’ll Love it:
- A higher environmental tolerance than other PCB surface treatments
- Works with fine pitch and small components
- Precision flatness due to immersion finish
- Compatible with wire bonding
Why You Won’t:
- Can cause solder mask aggressiveness
- High cost
- Risk for black pads on ball grid array
- It can lead to a signal loss in signal integrity applications
Electroless nickel electroless palladium immersion gold (ENEPIG)
This treatment utilizes various layers to achieve a universal finish that can support several applications, such as wire bonding or soldering with copper, aluminum, or gold. The name of the surface finish corresponds to the order of the layers over the substrate. An electroless nickel layer is also present over a copper base. And on top of that layer is an electroless palladium coating to stop the layer from passing through to the gold base on top. Finally, an immersion layer gold prevents the palladium from blending with environmental components that could impede soldering.
Why You’ll Love it:
- ENEPIG’s gold surface layer protects the board from corrosion
- It can meet strict requirements of various packages, including BGA, SMT, and wire bonding
Why You Won’t:
- Requires users to follow careful procedures (high-maintenance)
- High cost
HASL (Hot Air Solder Leveling)
HASL is the most commonly used PCB surface finish treatment. It involves dipping the circuit board in a solution of molten solder (tin/lead) and then using a hot air knife to blow off the residue. In between, the solder covers all the exposed copper surfaces on the board. Blowing high pressure hot air helps remove the excess solder and levels the solder deposit on the board surface.
Why You’ll Love it:
- Economical
- Supports all kinds of soldering or assembling (wave, manual, reflow, etc.)
- Reworkable with a long shelf life
Why You Won’t:
- Lacks the ability to hold tight tolerances on plated holes
- Not compatible with Chip on Board (COB) technology
- Won’t work well for surface mount device and ball grid array pitch of less than 20 mil
- At greater risk for bridging
Lead-Free HASL
Lead-Free HASL is different from HASL as it doesn’t use tin-lead solder. Instead, it relies on tin-copper-nickel germanium. This helps the treatment provide the highest level of solderability, as well as robustness with regard to storage and multi-step assembly at an affordable price. Another noticeable aspect of a lead-free HASL is that it’s less flat than other finishes.
Why You’ll Love it:
- Allows for multiple thermal excursions
- Highly solderable
- Economical
Why You Won’t:
- You’ll end up with a difference in thickness for the small pads vs. the large pads
- Requires high heat for processing (minimum of 260° C)
- Won’t work well for surface mount device and ball grid array pitch of less than 20 mil
- Greater risk for bridging
Immersion Silver (IAg)
Immersion Silver gained popularity after the WEEE and RoHS directives took effect. It’s a stable finish with a roughly 12-month shelf-life and has a simple process control. It’s often used for EMI shielding, aluminum wire bonding, and membrane switches. Because of the way silver and copper react, they ultimately diffuse into each other. Also, the process sometimes includes organic matter, which helps prevent silver from corroding and resolves the silver migration issue.
Why You’ll Love it:
- Suitable for BGA/smaller components
- It offers good stability
- Relatively inexpensive (mid-range)
- Allows for reworking
Why You Won’t:
- May lead to silver whiskering
- Requires special packing to keep it solderable
- Highly sensitive to tarnishing
- Not compatible with peelable masks
Immersion Tin (ISn)
Immersion tin is directly applied to the PCB’s base metal using chemical displacement. Tin is the most affordable form of immersion coating, and as with every other immersion coating type, a chemical process is involved. The flatness of this specific coating makes it an ideal surface finish technique for small components and geometries. Also, being a RoHS compliant surface finish, Immersion Tin is a great choice for fine pitch components.
Why You’ll Love it:
- Suitable for press fit
- Offers excellent flatness (20-40 micro inches in thickness)
- Provides good solderability
- Uses less chemicals and water in the application process
- Relatively inexpensive (mid-range)
Why You Won’t:
- Limited shelf life (3-6 months)
- Can lead to tin whiskering
- Must handle with gloves
- Not compatible with peelable masks
OSP (Organic Solderability Preservatives)
This technique produces a thin, uniform, and protective layer on the copper surface, which protects the circuitry from oxidation during assembly and storage. OSP is applied on copper pads to secure them before soldering. The treatment actually results in an organometallic layer securing the copper before the soldering process. And because it is water-based and organic in nature, the surface finish has a low carbon footprint.
Why You’ll Love it:
- Can be repaired
- Has a short process cycle
- Leads to a flat, co-planar surface
- Is lead-free
- More economical than metallic finishes
Why You Won’t:
- Has limited thermal cycles
- Can be difficult to inspect (no option for visual inspections)
- Requires gloves for handling
- Does not hold up well in the presence of moisture.
When it comes to choosing from these surface finishes, make sure to consider your production volume and requirements for cost, environmental impact, and durability. By gaining an understanding of the above attributes, you can be sure to choose the ideal PCB finish. Need help? Contact our experienced electronic manufacturing services team for assistance in picking the best finishing option for your project.