You know the old adage: “You get what you pay for.” You should heed that advice when it comes to PCBs.
Cheap PCB sourcing may look attractive, but it’s likely to cost you more in the long run. Besides poor-quality standards, cheap printed circuit boards bring with them unplanned, hidden costs.
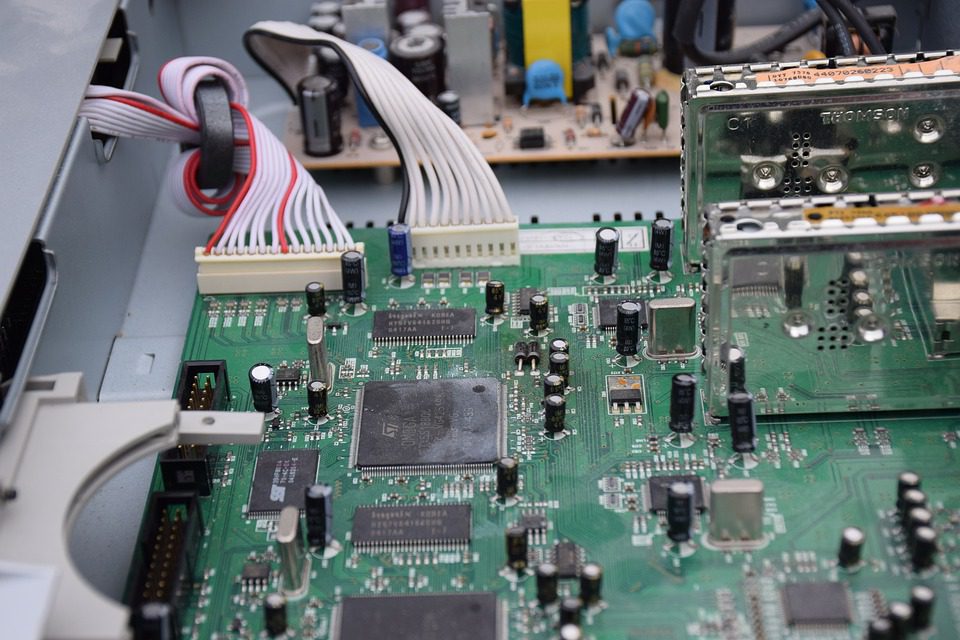
(Pixabay / FrankMagdelyns1)
We’re all for a good deal on PCBs, but a deeply discounted product should give you pause. Here’s why you should think twice before placing an order for an unusually cheap PCB import.
- Health hazards: Inferior PCBs come with health-related risks. For instance, certain vendors will incorporate metals and other cheap-quality components to reduce the cost of manufacturing. The issue with this approach is that the components are sometimes toxic, featuring substances like lead, mercury and cadmium. Substances like these could result in serious health hazards. To have peace of mind, you should always import PCBs that use ROHS-compliant components (Restriction of Hazardous Substances).
- Poor impedance: A PCB’s impedance has a major say in the RF performance of mobile phone boards. The common issue with cheap PCB imports is that the impedance variance between the board units is relatively large. The key to preventing this is to ask the supplier for general impedance test reports, but make sure to specify that you’ll need comparative data for different board sizes.
- Untested functionality: To reduce the cost of manufacturing, some PCB vendors will take shortcuts with testing. Instead of rigorously testing every aspect of the board, they’ll only test the basic functionality. While this does validate whether the product will function or malfunction, the more important aspects of the unit ship untested. This could have a damaging effect on your reputation should one of the untested components break after the PCB’s integration in a client’s device. In other words, if a PCB is not subjected to a rigorous quality assurance protocol, it could ruin future sales of the device it’s fixed in.
- Bad dimensioning and cutting: PCBs should be guaranteed to comply with the tolerances and dimension sizes the user needs. Unfortunately, cheap PCB manufacturers don’t pay much attention to this part of PCB production. Boards are often cut too small or too large, which hinders their ability to fit inside mechanical box assembly. A top-quality manufacturer will always check the mechanical dimensions of a PCB quality visually before proceeding any further.
- Solder mask issues: This is a common shortcoming of cheap PCB imports. Solder mask layers protect vias and copper through corrosive effects. They also mitigate solder bridging during PCB assembly and soldering. However, low-quality manufacturers often design footprint-pads close to each other, resulting in solder mask voids (solder cannot deposit in the empty area between the two pads). The issue could cause the PCB to be susceptible to malfunctions and short-circuiting.
- PCB “twist”: You may have also heard of this phenomenon referred to as “warpness,” and it is common to multilayer boards. Manufacturers who don’t care about thermal balance or temperature control produce printed circuit boards that experience this twisting or warping so that the PCB layers no longer stay flat. Reliable manufacturers, on the other hand, will manage heat increase rates while delivering grid support to the PCB. Warp needs to be avoided since it’s impossible to remove. In the long run, it may also cause copper-tracks cracks or breakage. During the assembly and component mounting process, the flatness of the PCB is crucial for mounting of components and solder paste decomposition.
With so many risks associated with cheap PCB imports, you could end up suffering more than just a financial loss. Think about all the ways your reputation, brand, and the final product could be affected due to the above issues.
Rather than trying to save money with poor quality PCB imports, take the smarter approach to cost-cutting by following these steps:
1. Stick to a Stable Procurement Strategy
Rather than sourcing your PCBs from a variety of vendors, create a stable procurement strategy by working with a few companies. This will lead to a gradual reduction in expenses. For instance, tooling costs will be saved when you reorder PCBs from the same assembler, resulting in long-term gains and progress.
2. If Possible, Skip Slots
Reducing PCB costs also comes with what you forgo. Don’t request internal cutouts unless you really need them to mount the board. Many vendors will increase the total on the invoice when they’re instructed to cut slots or make other cutouts in your PCB. While unique cutouts can be exciting for engineers, they won’t make much of a difference to your brand recognition or product functionality.
3. Order standard shapes
Try saving space when you can, but don’t narrow things so much that it requires multiple runs to get the PCB together. If you’re struggling to find balance, remember that ordering standard shapes is an ideal way to lower PCB costs. Standard shapes also provide you with component cost leverage.
Also, if there are quality issues with the components (which shouldn’t be the case if you work with a reliable manufacturer), you can choose another unit immediately.
Contact us today for reasonably priced but high quality PCBs. As a leading, U.S.-based contract electronic manufacturer, we can guarantee you a good deal coupled with all of the right quality inspections and certifications.