PCBs came around in the middle of the 20th century as an alternative option to wires. Since then, the electric circuits have become indispensable in the production of any electronic device. Naturally, engineers worked hard to improve the design, size and technical components of PCBs, which led to the birth of HDI technology.
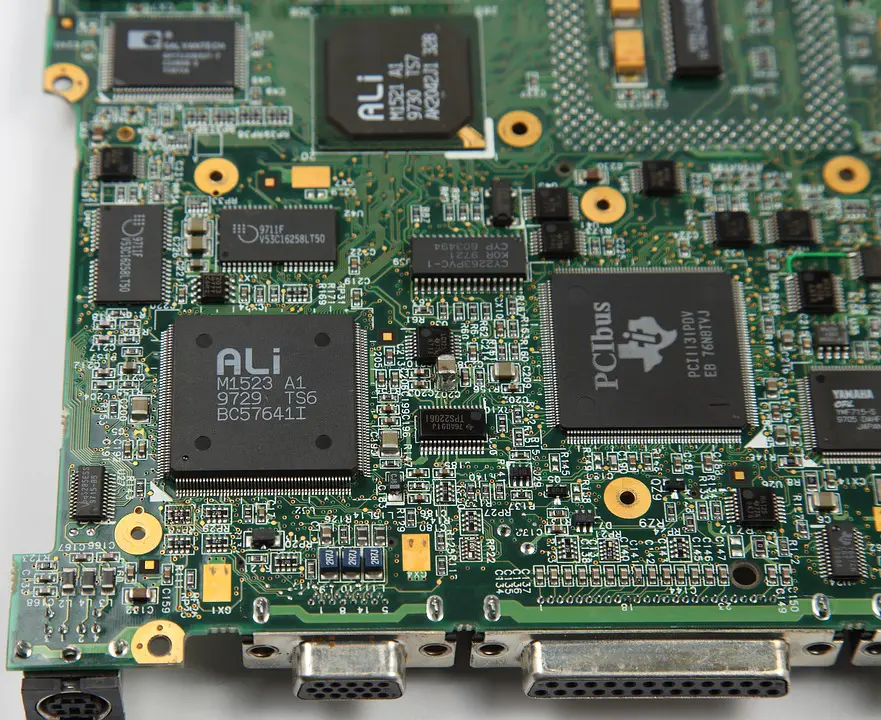
(Pixabay / nanoslavic)
HDI stands for High-Density Interconnect. It’s a type of PCB that has many interconnections fitted within a small space. HDIs give PCB designers the luxury to make smaller equipment with much more creativity. Despite the reduction in size, the efficiency of the equipment stays the same or multiplies in many cases.
In technical terms, any PCB that contains between 120 to 160 pins per square inch can be called an HDI PCB. Micro vias technology also became popular because of HDI PCBs and led to the development of dense circuitries. HDI PCBs have varying features, such as the capability to optimize redundant radiation impedance control, high-frequency transmission, and more. But the two key features that define an HDI PCB include versatile routing and component placement.
Difference between standard PCB and HDI PCB
When using small vias in HDI, you are able to reduce the stray capacitances and achieve better signal performance. The stray capacitance of normal vias in standard PCBs is much higher and therefore affects the signals. Moreover, HDI PCBs have more components per square inch compared to a standard PCB. Standard PCBs are heavier, whereas HDI PCBs are lighter in weight. HDI PCBs also have a high pin count, but standard PCBs face compatibility issues in this case.
Benefits of HDI PCBs
HDI PCBs are lighter, smaller and more compact, so they are a great pick for any device designer. Below are some of the main benefits of using HDI PCBs in manufacturing:
Compact
It’s hard to neglect HDI PCBs because they’re a compact and well-rounded option compared to standard PCBs. The trio of micro vias, blind vias and buried vias help in creating a better electronic device.
Better Signal Transmission
HDI PCBs help in reducing the path length of signals for quick transmission. This is because circuit components are closer in an HDI PCB.
Reliable
PCB technology brought more rigidity to electronic devices because these boards are designed to stand the test of time. However, HDI PCBs take this to the next level by using stacked vias. This creates an extra shield of protection for the circuitry and adds more reliability to the device.
Pocket-friendly
Reduction in component layers makes it easy to carry devices around without worrying about weight and size. Four layers of HDI PCBs are good enough to perform all the functions of a standard PCB.
Low Power Consumption
A higher number of transistors and a smaller distance between components can lead to better electrical performance. Features like these allow for low power consumption.
Uses of HDI PCBs
HDI PCBs have a widespread application in various fields of life. Let’s look at a few areas where High-Density Interconnect PCBs make a difference:
Healthcare
Medical industry PCB designers are currently borrowing from the latest innovations in HDI PCBs, especially in terms of size. Most medical devices now incorporate HDIs since they are small and fit in implants as well as imaging equipment. These devices play a major role in diagnosing and treating diseases, so smaller chips require less intervention. For example, a heart pacemaker is a device that attaches to the human heart and maintains circadian rhythms. Smaller HDIs enable researchers to produce smaller pacemakers with more efficiency.
Another example is the colonoscopy camera that passes through a person’s colon for medical examination. People often avoid colonoscopies due to the painful side effects, but a smaller camera with better visual quality can make the procedure less painful, increasing the number of people who get this critical procedure.
Automotive Industry
Cars and other vehicle manufacturers are very attracted to HDI PCBs because much more innovation is possible with the help of these chips. You can save more space in a vehicle and increase its performance with HDI PCBs. Futuristic and hybrid cars like Tesla use PCBs to run their electronic functions that extend battery life. Other devices like tablets and smart assistants fit easily within the vehicle dashboard as well, thanks to HDI PCBs.
Digital Devices
Compare today’s digital devices like smartphones with those of 5 years ago. You will notice a significant difference in size as well as weight. This shift was made possible with HDI PCBs in ELIC (Every Layer Interconnection) construction. Thinner, more portable devices and new developments like smartwatches owe their existence to HDI PCBs. VR Headsets and fitness bands also use HDI PCB technology to fit the latest features into a small device.
Aerospace and Military
Strategic equipment like missile and defense communication systems use HDI because it is the most versatile solution on the market. The aerospace/defense fields are constantly changing, and HDI PCBs accommodate evolving needs. Every gadget you can dream up in this industry contains a tiny PCB to perform one function or another. Other communication devices like wireless phones, trackers and cameras are becoming smaller in size, and some contain up to 10-layer HDI construction.
So now you know some major arenas where HDI PCBs shine. However, it’s still crucial to keep its costs in mind when determining your budget. Below are some of the main factors that impact HDI PCB’s pricing:
Number of layers – Additional layers and the type of stackups you require will impact the price. For example, 2-n-2 HDI board layouts are more complex than their 1-n-1 variants, so they’ll probably cost you more.
Materials – You have many choices when it comes to the type of material your HDI PCB incorporates. You can choose from fiberglass, metal, FR4 or other material based on the application of your board, and your final price tag will vary accordingly. Immersion silver, HASL, ENIG, gold, and immersion tin are some of the choices for surface finishes. Most HDIs feature ENIG because of its flatness and solderability.
Stacked/Staggered – You might also find price variations between staggered and stacked variants. Staggered vias can’t be filled with copper, whereas stacked vias accommodate filling and typically require more hours for finishing.
If you need help knowing if HDI PCBs are right for your product, and which type you should choose, contact us for help. As a distinguished contract electronics manufacturer, we can help with all of your PCB and PCBA questions and needs.