Ever find yourself juggling multiple PCB interfaces just to decide which one to incorporate into your circuit design? You’re not alone. A lot of PCB designers struggle to know which functionality would be best for the project at hand.
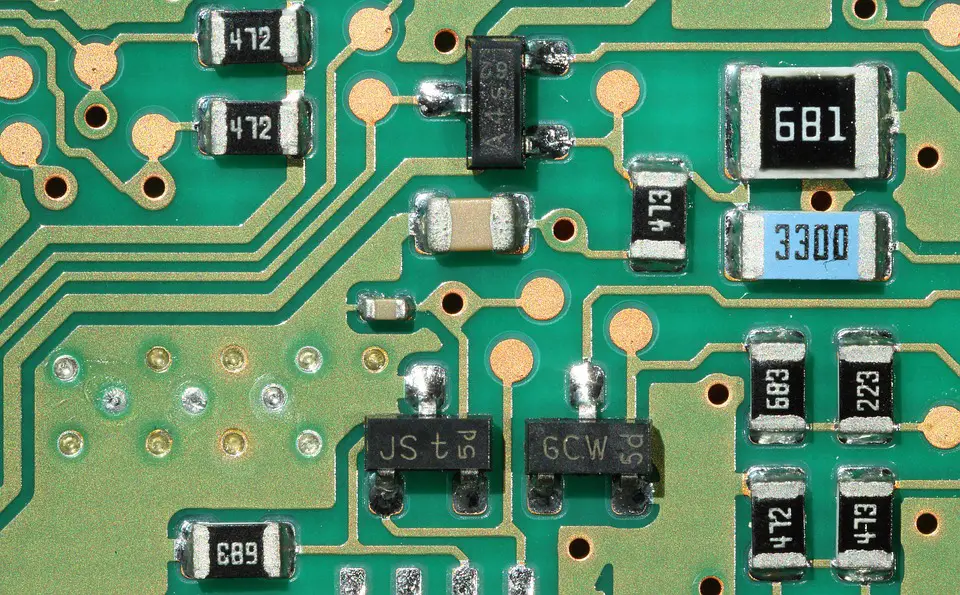
(Pixabay / 2427999)
This article covers the most commonly used interface types in PCB circuits, along with the purpose they serve. By the time you get to the end of this post, you’ll be in a better position to decide which interface to use in your next project.
Commonly Electric Circuit Interfaces
RS-232 connection
RS-232 is the EIA (Electronic Industries Association) standard for interchanging of binary data between different devices. The standard enables as much as 20 signals to be defined, but the user has complete freedom. Its physical characteristics feature both a 25 and 9 pin D connector. The interface is capable of operating at high data rates where the area is short. Voltage levels for RS-232 are labeled as a range from “-12 to +12” volts. PCB users need to be aware of RS-232’s shortcomings, with shorter transmission distances and speeds being one of the major concerns.
That being said, the protocol is an option to consider for circuit design. It allows data rates of up to 20 kbps. Rates can be transferred through cables as long as 15 meters. Control circuits are typically used for managing connections between DCE and DTE, and a hardware circuit known as URAT is used to control the serial ports.
Emitter Coupled Logic design
ECL was considered to be the fastest logic family in the 70s. Even today, it runs fast enough and can clock up to hundreds of MHz. Part of the credit for its performance goes to BJT (bipolar junction transistor) within the logic, which doesn’t saturate when activated. This enables the speed of work to be enhanced naturally. The setup also allows the transistors to work in their linear active operational region and thereby, they don’t have to deal with charge storage times. This makes the gate work at high speeds, and this is the main benefit of using the ECL interface.
But, like with other interfaces, there’s an opportunity cost. In the case of ECL, it’s the large power consumption. This creates EMI-related issues and also reduces the anti-interference ability. If you can compromise on these two things, then ECI might be a good option for you. Do note that a special level shift circuit will be required as the circuit runs on a negative output voltage.
Optical Isolation connection
This is a versatile interface that’s typically placed between a receiving electronic and a sensor. Its main function is to deliver an electronically robust output to the end device. It’s an excellent choice for devices with poor signal support, grounding and/or noise issues. The optical isolator offers a clean interface that is used to lower signal degradation from long cable runs, remove ground loops, and more. It accommodates differential and single inputs and offers outputs of the same in either linear driver or open collector configurations, accommodating voltages from 5-28 VDC.
Under the scenario where the circuit needs to function at a high frequency, only this interface can meet the requirements of data transmission.
Transistor-Transistor Logic design
TTL logic designs involve bipolar transistors acting on current pulses. TTL-based devices make use of transistors with various emitters in gates where there are multiple inputs. They’re commonly immune to noise and are known for high-speed switching. The main downside of using this interface is that it draws a lot more current than similar circuits featuring MOS logic.
TTL’s driving capacity can go up to tens of milliamps while its speed is typically around 30 MHz. Normal operation will generally involve a high signal voltage, and when placed near ECL circuits with lower signal voltages, more issues could arise. Low-current TTL interfaces may be your best bet to avoid crosstalk problems.
Conclusion
As you can see, there are various PCB interfaces available for circuit design, and each of them has their own advantages and limitations. When it comes time to pick an interface, be sure to assess your needs and where you can compromise to make the best design.
And if you still have questions, make sure to talk to the design team of your contract electronics manufacturer. Their in-depth experience can help guide you and ensure that you make the best choice possible.