Electronic manufacturing services (EMS) or electronics contract manufacturers (ECM) build and provide manufactured electronic products and components. Primarily, these are the companies responsible for building circuit boards for electronics used in every industry. More recently, they have become more involved in the aftercare portion of the production. They know how to build, test, and maintain almost any electrical product.
Being able to do all these things requires a large array of equipment. Technology is constantly advancing, so all EMS companies must keep themselves up to date. Doing so ensures that they can fulfill any order and keeps costs down for buyers.
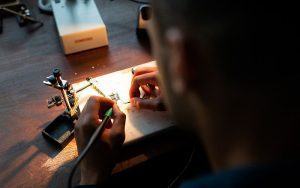
(RAEng_Publications / pixabay)
So if you’re looking to team up with an electronic printed circuit board assembly service provider, make sure they have the following equipment at their disposal.
Solder Paste Printing Machines and Solder Paste Inspection (SPI) Machines
A far cheaper option than drilling, solder is used to install components onto any PCB. Solder is a paste made of a composition of metal alloy particles. Generally, tin, lead, and silver are used due to their high levels of conductivity. Solder has many benefits in PCB construction, particularly how it helps to dissipate heat buildup through the board’s layers.
Any EMS needs to own and operate solder paste printing machines. These machines follow pre-stenciled paths on blank boards and mark out where the solder will go. A squeegee will then apply precise amounts of solder to the marked locations. After, the machine will drag a special blade across the board, ensuring all solder is spread evenly. The board is then ready to have the components applied.
Equally as important, a solder paste inspection machine will then be used. The soldered boards will be input into the SPI machine, where it will measure each solder area for:
- Volume
- Size
- Height
- Alignment
Spotting these errors at an early phase will help prevent any necessary reworks later in production. These cuts in costs and lost time will allow for a greater number of PCBs to be produced.
Glue Dispensing and Pick-and-Place Machines
To counteract any potential dislodging during the manufacturing process, small glue dots are used to hold the components in place. A glue dispensing machine applies these dots to precise locations quickly and efficiently. Loose components can easily move around a board until they are soldered into place. From here, the PCB can be passed along to a pick-and-place machine.
A pick-and-place machine is a faster and more precise method of building PCBs than to do it by hand. The machine does exactly what its name implies: it picks specific components from a store and places them on the board.
Exact specifications are input into the machine, allowing for the quick and precise placing of components. The average pick-and-place machine can place up to 30,000 components per hour. The components are placed onto the glue dots, which hold them where they need to be, and the board is ready for soldering.
Reflow and Wave Soldering Machines
There are two different ways (and thus two different machines) that the components are soldered fully to a PCB. Most often, an electronic manufacturing service will use one or the other.
Reflow soldering is the more widely used of the two. Once the components are in their positions, the incomplete PCB is fed onto a conveyer belt. The belt passes through several variable temperature zones, where the solder is melted where it was set. The component connectors will sink into the solder, setting solid again when it enters a cooler zone. At this point, the circuit will have been formed, and the components all connected.
The alternative to this is wave soldering. In this form, a prepared PCB is passed over a pool of molten solder. The solder connects with the underside of the PCB and attaches itself to exposed component leads or contacts. The wave is receded, and the contacts are left to dry, forming a solid connection.
Reflow soldering is the more popular of the two for many reasons. There is no need for any through-hole components with reflow, as everything is soldered on the surface. It also allows for more precise solder points, as the solder is only found previously applied. In these ways, it is more suitable for mass production.
However, wave soldering does have its advantages. Wave soldering means a much lower chance of any heat damage occurring without exposing the PCB to heat. The solder joints are also more secure, as more solder is used, and none is lost in transit.
Inspection Machines
Once the PCBs have been assembled, the final stage of production is to inspect and test them. Several different machines can help in this process: Automated Optical Inspection (AOI), In-Circuit Testing (ICT), and Function Validation Test (FVT).
- Automated Optical Inspection (AOI) – While most defects can be spotted with the naked eye, an AOI machine helps to mitigate any potential mistakes. This machine uses a high-definition camera to capture an up-close image of the completed board. This image can then be compared with others to highlight any errors or problems.
- In-Circuit Testing (ICT) – The bed of nails involves a layout of spring-loaded pins on which the finished PCB is placed. The pins make a circuit with many connection points. This completed circuit is used to test the connections and find any breaks or shorts in the PCB. From here, the team can repair any issues or faults.
- Functional Validation Testing (FVT) – The PCB is hooked up to a functional system and loaded with software in this final test. A diagnostic test is run, using the board as it would function in a final product. If everything is functioning right, the software will load correctly. If any defects or failings occur, the tester can determine which aspect of the board is causing the problem and replace or fix it.
Conclusion
The process for building PCBs and other integral electronics parts is intricate. In the old days, teams of engineers would dedicate hours to manually putting together a single board. Now, with advancements in machinery, hundreds of boards can be assembled and tested in a single day. Any company looking to work with an EMS partner would benefit from ensuring they have the right equipment for the most efficient PCB assembly.