With each passing day, computer technology becomes more integrated into everything we do, to the point that almost every device in our homes contain several specially designed printed circuit boards. Today, we’ll shed light on halogen-free printed circuit boards, which differ from the standard PCBs that most people are familiar with.
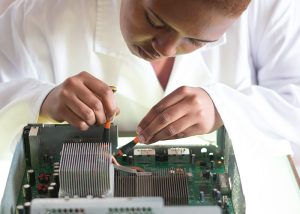
(RF._.studio / pexels)
What Are Halogen-Free PCBs?
As the name suggests, halogen-free PCBs are boards made using components that do not require or contain halogen in their construction. Any piece that contains certain amounts of the elements bromine (Br), chlorine (Cl), fluoride (F), or iodine (I) falls under the category of made with halogen. However, as long as the amounts of these chemicals stay below 0.09% wt (weight-ratio), you can label these boards halogen-free.
Why Were Halogen Boards Used?
The chemicals used, particularly chlorine and bromine, were added due to their flame-retardant properties. The halides (halogen materials) were known as PBB and PBDE. Copper cladding containing these elements was applied to help protect the board and its components from heat damage.
Engineers later discovered that halogen PCBs emit large quantities of highly toxic gas when burned. This gas smelled unpleasant and, when inhaled, had carcinogenic properties. The gas was also harmful to the environment. For these good reasons, electronic manufacturing services began seeking alternative ways to construct PCBs. The European Union and China have even gone so far as to ban halogen-containing PBB and PBDE use in PCB cladding.
What are the Alternatives?
Instead of using PBB and PBDE cladding, halogen-free PCBs mainly employ phosphorus and phosphorus-nitrogen. Unlike halogen, when phosphorus burns, it undergoes thermal decomposition to become a polyphosphoric acid. This substance then dries and hardens against its surface to create a carbonized film. It does all this without releasing dangerous gasses or harming anyone or anything nearby while also helping to put out the source of the fire by depriving it of oxygen.
For devices using phosphorus-nitrogen, a similar effect occurs, except they release a non-combustible gas. This gas aids in retarding the fire like the polyphosphoric acid.
What are the Benefits of Going Halogen-Free?
Aside from being better for the environment and less toxic for users, building halogen-free PCBs offers many other benefits. As PCBA manufacturers become more eco-friendly and seek alternatives to halogen PCB resins, more reasons to switch to halogen-free boards have come to light. Some of these are:
- Better insulation for the board – The polarity of the molecular bonds of halogen is greater than that of the alternatives used now. As a result, non-halogen resins improve insulation resistance within the circuitry and reduce the current’s break-down rate.
- Less water absorption – Halogen molecules have more electrons than phosphorus-nitrogen, meaning they are far more likely to bond to water molecules. This also means that halogen-free PCBs have a higher resistance to water absorption. While at a much smaller scale than a PCB is likely to encounter, halogen-free PCBs are better able to handle wetter environments and situations.
- A higher TG – TG is the point at which glass melts. Halogen-free boards have a much higher TG than traditional ones, which can withstand higher temperatures. This makes them better for use in higher-power designs and applications.
- Better thermal stability – Halogen-free PCBs have a higher monomer molecular weight, meaning that their molecules are far less mobile. This reduced mobility prevents halogen-free PCBs from expanding under heat as much, providing a greater degree of stability.
Negatives of Using Halogen-Free PCBs
Of course, switching to halogen-free comes with its downsides. Though not as numerous as the benefits, some cons include:
- More expensive than traditional PCBs – Halogen-free PCBs require specially designed chemical resins, and they are not as easily or widely produced as the PBB and PBDE claddings are. This means the companies that provide these will generally charge more for their product.
- Fewer manufacturers provide them – Far more manufacturers provide traditional PCBs than halogen-free ones. This will limit the number of available purchase options and require greater care and attention when finding a fully competent supplier with the techniques.
Common Uses for Halogen-Free PCBs
Halogen-free PCBs are becoming more common in everyday applications. As the range of electronic devices continues to grow, the number of halogen-free PCBs in use is rising. Some of the devices currently operating on halogen-free PCBs include:
- High-end computers and large server farms
- Mobile phones and other wireless devices
- Signaling and trafficking devices
- Consumer electronics such as televisions and games consoles
- Transportation applications such as GPS and onboard computer devices
- Power stations and substations
- Laboratories
- Distribution and sorting rooms
Since government incentives are driving companies towards greener alternatives, it is safe to assume that the number of uses for halogen-free PCBs will only continue to increase.
A safer and more eco-friendly alternative to traditional PCBs, halogen-free PCBs represent a shoo-in for a future standard. Whether looking at new boards for upcoming devices or setting up a business building the ideal halogen-free PCB, more companies will soon pick up this latest and safer advancement in PCB assembly.